CASE STUDIES
May 17, 2018
LONG CLAMPING SOLUTION
Situation
An automotive parts manufacturer approached PML-PAL engineering with an unusual work piece shape (see photo below). Due to its unique geometry, it was impossible to clamp it one time to complete the machining job. The customer held it in a conventional way on the outer diameter for the first operation, then on the inner diameter for second one, using two machines. Total machining time was two minutes.

Challenge
The work piece was going to be mass produced and a robot needed to be integrated in the loading process. There was a need to come up with one clamping solution to
overcome those challenges and reduce time.
Solution
PML-PAL engineering using newer methodologies, worked closely with the customer to design a unique chuck that clamped the work piece from the long inner diameter.
The solution provided a long clamping system to support the work piece from both ends and hold it stable far from the chuck's face. The chuck provided one clamping
solution that allowed the customer to finish the part in a single machine.
Results
The customer is now able to produce parts continuously without human intervention. The process is completely automated. The chuck is able to spin at relatively high
speed of 2000 RPM while turning. It allows an independent robot to access the work piece to replace it with another for continuous operation. The PML-PAL solution cuts
the process to one operation in one turning machine and reduces the total machining time to one minute. Overall, the savings is approximately 50%. As a result of their
high satisfaction with this job, the customer asked PML-PAL to produce two more identical chucks for two additional machines. Today, the plant runs three machines,
three shifts, 24/6.
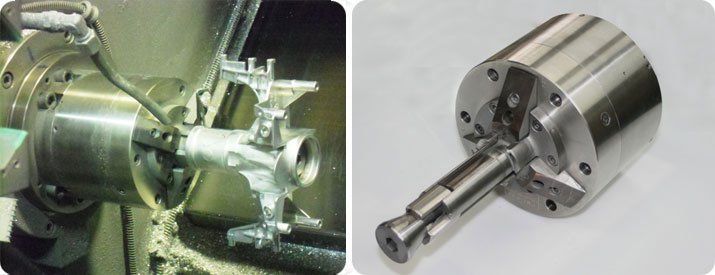